Compaction Grouting ist eine besondere Herstellungsvariante des CMC®-Verfahrens mit angepasstem Säulendurchmesser für locker gelagerte Sande und stark geschichtete Böden.
Verdichtung und seitliche Verspannung von Böden durch Materialzugabe
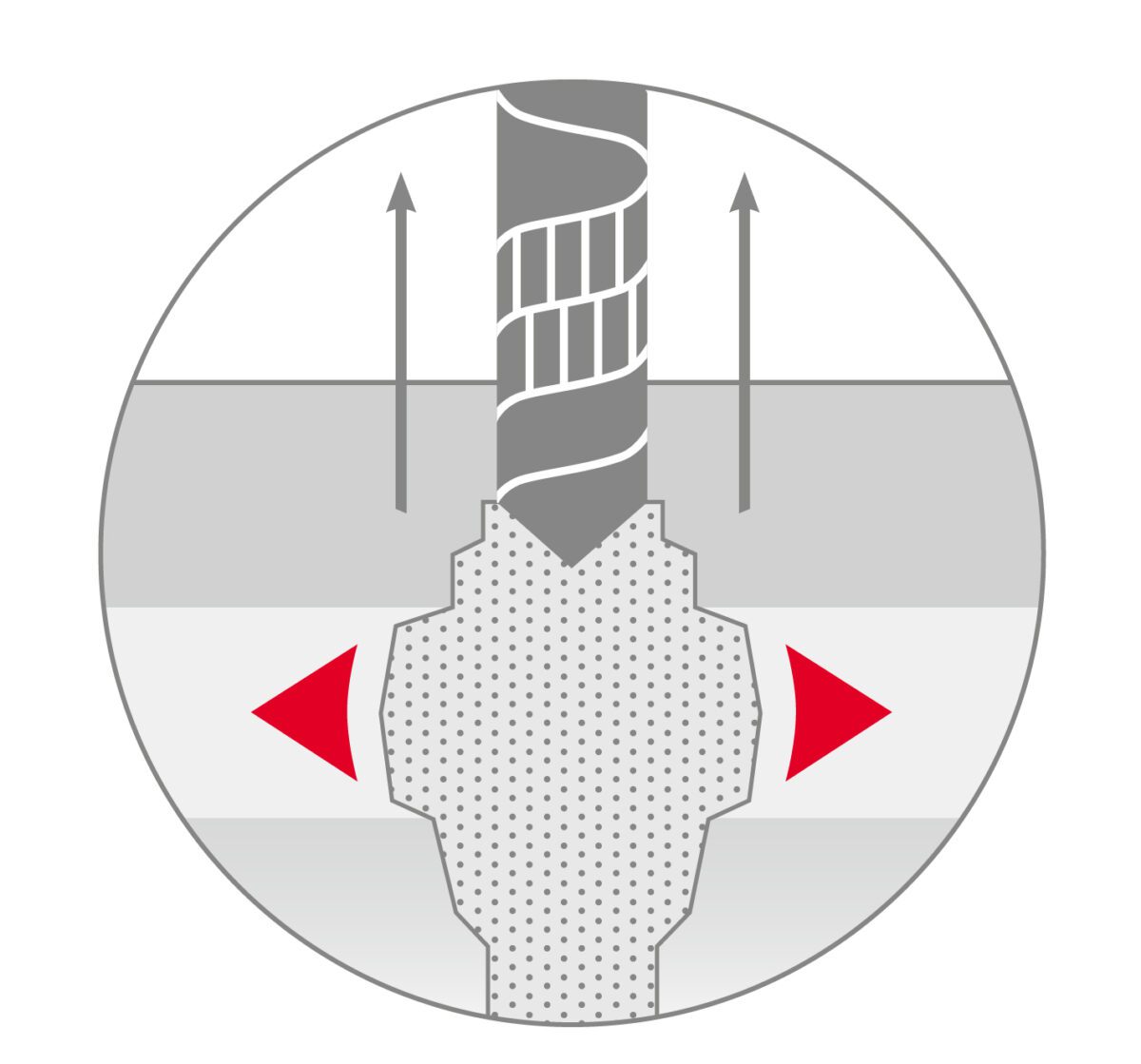
Mit Compaction Grouting haben wir einen besonderen Fokus auf die schichtenweise Verdichtung des Bodens. Hierzu pressen wir bei der Herstellung der Säulen einen Zementmörtel unter erhöhtem Druck ein, bis ein festgelegtes Einpressvolumen erreicht ist. So verdichten wir den umgebenden Boden und erzeugen vertikale Säulen mit variablem Durchmesser. Diese können auch als Tragelemente zur Gründung eingesetzt werden.
Key facts des Verfahrens
Tragwirkung und Bemessung
Die Bemessung des Compaction Grouting Verfahrens kann auf zwei Weisen erfolgen: Sobald durchgängige Säulen hergestellt werden, können diese analog zu CMC® mit Ansatz der vertikalen Tragwirkung bemessen werden. Zum anderen wird die Verdichtung und Verbesserung des Bodens zwischen den Säulen anhand des definierten Einpressvolumens je Schicht berechnet.
Anwendungsbereiche
- Verminderung des Verflüssigungspotenzials locker gelagerter Sande
- Verbesserung und seitliche Verspannung stark geschichteter Böden
- Erhöhung der Lagerungsdichte bei nichtbindigen Böden
- Verbesserung der Konsistenz bei bindigen Böden
Vorteile Compaction Grouting-Verfahren
- effiziente Verdichtung in geschichteten Böden
- Verdichtung einzelner Schichten auch ohne durchgängige Säulenherstellung möglich
- keine Entsorgungskosten für Bohrgut
- vibrations- und erschütterungsfrei – herstellbar in direkter Nähe zu Bestandsbauwerken
- vertikale Tragelemente reduzieren die Belastungen auf den umgebenden Böden
Anwendung und Methode
Compaction Grouting ist eine Herstellungsvariante des CMC®-Verfahrens mit besonderem Fokus auf die Verdichtung des umliegenden Bodens. Wie beim CMC®-Verfahren teufen wir den Vollverdrängungsbohrer mit großem Drehmoment in den zu verbessernden Boden ab. Nachdem die erforderliche Tiefe erreicht ist, ziehen wir den Bohrer schrittweise nach oben und pressen unter erhöhtem Druck einen Zementmörtel ein. Der umgebende Boden wird dabei seitlich verdrängt, bis das vorher festgelegte Einpressvolumen je Bodenschicht erreicht ist.
Neben dem Verdichtungseffekt entstehen vertikale Säulen mit angepassten Durchmessern. Der Säulenquerschnitt hängt maßgeblich von der Steifigkeit und Schichtung des umgebenden Bodens ab. Zudem weisen die Säulen eine eigene Tragfähigkeit auf und können als Tragelement dienen.
Für einen optimalen Verdichtungseffekt erfolgt die Ausführung in mehreren Phasen. Zur Sicherstellung einer flächigen Verbesserung arbeiten wir die Ansatzpunkte in einem sich stetig verengenden Raster (Primär-, Sekundär-, Tertiärraster usw.) ab.
Beispielhafte Herstellreihenfolge Compaction Grouting
Verfahren
Beim Abteufen des speziell entwickelten Vollverdrängungsbohrers findet die erste seitliche Verdrängung des umgebenden Bodens statt. Die eigentliche Verdichtung erfolgt beim Herausziehen des Bohrers. Dabei injizieren wir einen hochviskosen Zementmörtel unter hohem Druck in das Bohrloch. Das Einpressvolumen steuern wir über den Durchfluss des Mörtels und die Ziehgeschwindigkeit des Bohrers. So sind Anpassungen an unterschiedliche Bodenbeschaffenheiten und -schichten möglich.
Im Vorfeld der Arbeiten wird in der Regel ein Kalibrierfeld angelegt, um folgende Ausführungsparameter festzulegen.
- Mörtelmischung
- Druck- und Injektionsstärke
- Ziehgeschwindigkeit des Bohrers
- Anzahl der Ausführungsphasen, Rastermaß und Ablauf der Ausführung
- Beurteilung der erzielbaren Bodenverdichtung durch die in situ Messung
Geprüfte Qualität
Die Qualitätssicherung und -kontrolle erfolgt wie beim CMC®-Verfahren durch digitale Aufzeichnung der maßgebenden Herstellparameter. Diese werden mit Herstellprotokollen dokumentiert. Das Verdrängungsvolumen zeichnen wir tiefenabhängig anhand des eingepressten Injektionsgutes auf.
Die Messung der Steifigkeit zwischen den Säulen kann mit dem Pressiometer erfolgen.